Choosing an Abrasion-Resistant Elbow:
What to Know
Abrasion-resistant elbows are an essential component of many pneumatic conveying systems, especially when conveying abrasive material such as green sawdust, wood chips, grains and seeds, and dry raw materials such as plastic pellets, sand or cement powder. Choosing the right type of elbow for your application will improve the longevity of your system and reduce problems such as plugging and blockages.
What is an abrasion-resistant elbow?
Abrasion-resistant elbows, also known as wear-resistant elbows, are used in industrial piping and conveying systems to connect pipes at an angle, while providing improved resistance to abrasion and wear. They are typically used in applications where the fluid or material being transported is abrasive, such as in milling, woodworking, agriculture, food processing, mining, mineral processing, sandblasting, and other heavy-duty industrial applications. Abrasion-resistant elbows are needed to ensure that the elbows are not worn through quickly by the abrasive materials being transported. In a pneumatic conveying system, air—and the material being carried by the air—hits the heel, or back of the elbow, at a high velocity before making the turn, resulting in increased wear at turning points in the system. An abrasion-resistant material extends the life of the elbow.
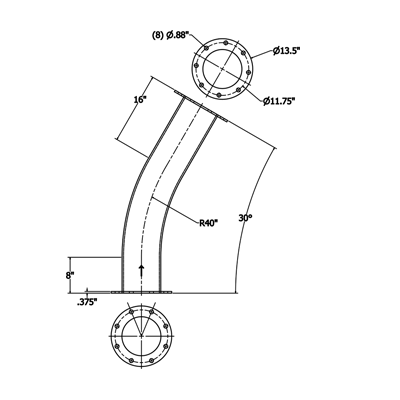
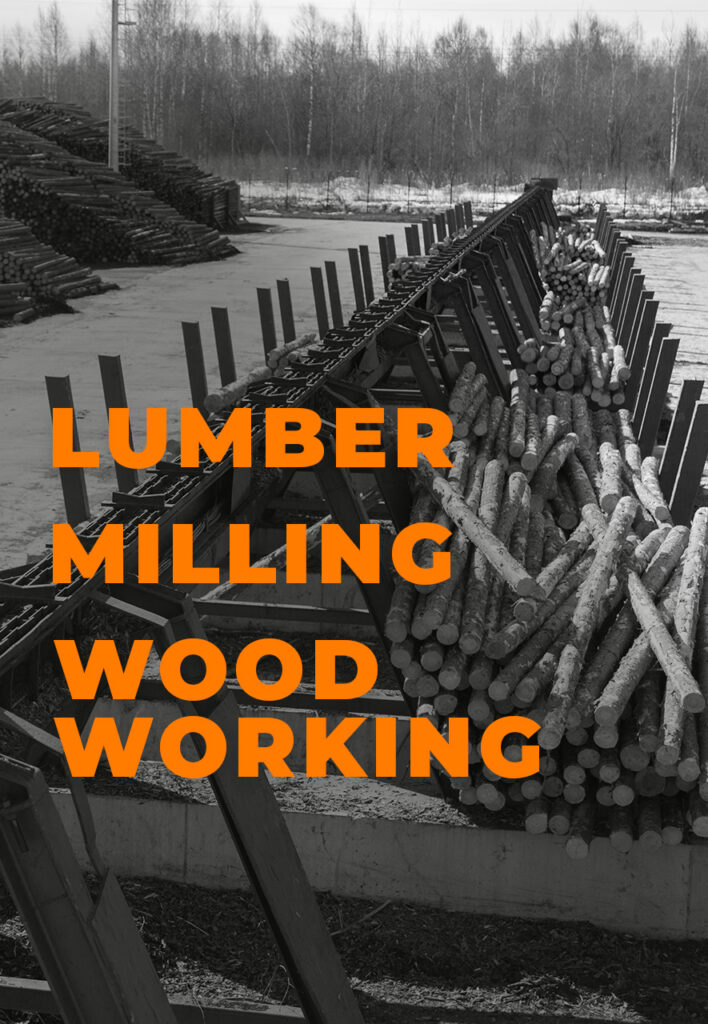
How are abrasion-resistant elbows used in the lumber, milling and woodworking industries?
In the lumber, milling and woodworking industries, abrasion-resistant elbows are commonly used for conveying green sawdust, chips and shavings from saws and planes to the kiln, where it is used as fuel, or to bins for collection. Typically, several elbows are needed in a conveying system for a sawmill or woodworking facility. Green sawdust is highly abrasive and will wear through standard piping material quickly, especially at the elbows. Choosing the right abrasion-resistant elbow will reduce maintenance requirements and total lifetime costs for the system.
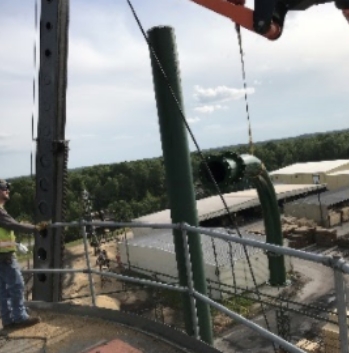
Where else are abrasion-resistant elbows used?
Abrasion-resistant elbows are used for pneumatic conveying systems in a range of industries, including mineral processing, chemical manufacturing, plastics, agriculture and food processing. Materials conveyed by these systems include grains, seeds, plastic pellets, chemicals and raw materials, sand, cement powder and other dry, lightweight material. Abrasion-resistant elbows are typically used in any pneumatic conveying system used with abrasive dry materials.
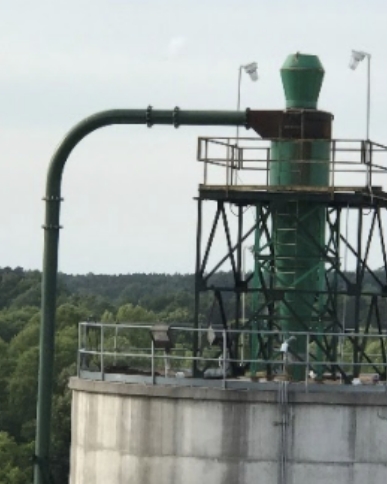
What kinds of abrasion-resistant elbows are used for pneumatic conveying?
Traditionally, flat-back (or wear-back) elbows have been used in sawdust conveying systems for milling and woodworking and for pneumatic conveying in other industries, such as agriculture, manufacturing and mineral processing.
Wear-back elbows are reinforced at the elbow heel to allow for added wear. A flat-back elbow has a flat-backed, removable section at the heel of the elbow, which is designed to be replaced as it wears out. These elbows require frequent maintenance and may need to be replaced as often as every six months.
Induction-hardened steel elbows are increasingly used in lumber, milling and woodworking and other industries to extend the life of conveyance system elbows. These wear-resistant elbows have an interior hardness of 600 Brinell, which leads to superior service life and performance. Induction-hardened steel elbows can last as much as much as 4x as long as traditional flat-back or wear-back elbows.
Induction-Hardened Steel vs. AR 235 and AR 400
Abrasion-resistant (AR) steel alloys, including AR 235 and AR 400, are commonly used in applications where the materials will be subject to high wear and tear, such as lumber yards, mining, mineral processing, and other heavy-duty industrial applications.
- AR 235 steel is a low-carbon, high-manganese alloy that is known for its resistance to abrasion and impact. It has a Brinell hardness rating (BHR) of about 235. AR 235 has better formability and impact resistance than AR 400 and is the most common choice for steel in wear-back or flat-back elbows.
- AR 400 is a high-carbon alloy steel with a hardness rating of about 400, making it much harder and more abrasion resistant than AR 235. However, it is more expensive than AR 235 and also less formable.
In contrast, induction-hardened steel has a BHR of 480-650 Brinell, making it much harder than AR 235 or AR 400. (The interior hardness of our Ultra Air induction-hardened elbows is 600 Brinell). This exceptional hardness results in better abrasion resistance, durability and longevity. Crucially, induction hardening only impacts the surface of the material, leaving the core more malleable. In the case of induction-hardening piping and elbows, this means the interior surface has an exceptionally high hardness level, while the outer surface of the pipe remains workable and weldable.
What are the advantages of an induction-hardened abrasion-resistant elbow?
An induction-hardened elbow provides several advantages over traditional flat-back or wear-back elbows.
- Longer service life: An induction-hardened steel elbow lasts up to 4x as long as a traditional flat-back or wear-back elbow, eliminating the need to frequently replace the elbow heels along with the associated material and labor costs.
- Better fit: A flat-back elbow has a rectangular cross-section, which makes it difficult to get a good seal between the elbow component and the circular pipe it is attached to. This can lead to leaks and added wear at the seams. An induction-hardened steel elbow, which has the same circular profile as the pipe it is fitted to, eliminates these problems.
- Improved performance: The smooth interior surface and superior fit of an induction-hardened steel elbow reduce the incidence of plugging and blockages at the elbow, further reducing maintenance requirements.
- Reduced costs: The total lifetime costs of an induction-hardened steel elbow are much lower than those for a flatback elbow made of AR 235 or AR 400 steel.
What is centerline radius, and how does it affect wear for pipe elbows?

The centerline radius of a blowpipe elbow is the distance from the arc of the elbow to the center of a circle that the arc follows. Thus, a long radius would have a long, gradual sweep, and would take up a lot of space. A short-radius elbow would have a tighter bend and be more compact. A more gradual sweep (longer centerline radius) reduces the impact of material on the elbow wall. Larger, longer sweep elbows tend to wear less and last longer than shorter radius, more compact bends. The longer sweep bends also reduce system back pressure and reduce the chance of material plugging.
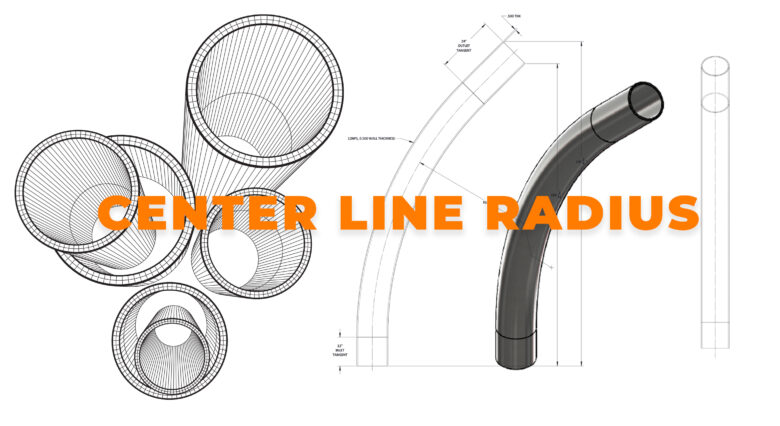
Ultra Air Standard bends utilize a centerline radius of 5x the diameter. Ultra Air Long Radius bends utilize a centerline radius of 12x the diameter!
Considerations in Abrasion-Resistant Elbow Selection
When selecting a wear-resistant elbow for pneumatic conveying, there are several important considerations to keep in mind.
- PERFORMANCE: For high-velocity, high-pressure conveying systems, the elbows can be a frequent cause of plugging, blockages and leaks. In addition to driving up maintenance costs, problems with the conveyance system can cause unanticipated downtime and reduce overall productivity. Induction-hardened steel elbows minimize these problems and maximize uptime for the conveyance system.
- LONGEVITY: Wear-back and flat-back elbows, by design, require frequent replacement of the wear-back heel. A longer-lasting elbow, such as an induction-hardened elbow, eliminates the time and costs associated with wear-back maintenance and replacement. Induction-hardened elbows can last up to 4x as long as an AR steel flatback elbow.
- COST: When considering cost, it is important to look at the total lifecycle cost for the elbow, including initial material and installation cost, replacement part material and installation costs, and the cost of downtime associated with replacement. A cost comparison of wear-back elbows vs. induction-hardened steel elbows shows that induction-hardened elbows have significantly lower costs over a two-year period. See the cost comparison.
- EASE OF INSTALLATION: How easy is it to install the abrasion-resistant elbow? The geometry of flat-back elbows can make achieving a proper fit problematic. In addition, heavy AR plate used in flat-back elbows is very difficult to form. This can make installation of the flat-back problematic. An induction-hardened elbow is easier to fit and install.